A Study of Delamination Under Various Loading Conditions
Wind turbine blades are typically manufactured from fibre-reinforced polymer (FRP) composites, and delamination failure can be an important issue in these structures. In extreme conditions, such as ice impacting, multiple delamination with a triangular shape is found in different parts of a blade. This delamination introduces local damage, which can then cause catastrophic failure under various loading conditions including buckling. Buckling and post-buckling are two loading conditions that can occur in large wind turbine blades due to gravitational, aerodynamic and centrifugal forces. In the work reported here, experimental studies of buckling and post-buckling failure in multi-delaminated composite beams were carried out. Laminated composite beams were pinned through their thickness using natural flax yarns to control delamination failure during the post-buckling process. Multi-delaminated composite beams were manufactured with laminate designs of [C90/G90]4 and [C0/G0]4 and tested to find the critical buckling load and post-buckling failure mode.
By Dr Hessam Ghasemnejad, School of Aerospace and Aircraft Engineering, Kingston University London, UK
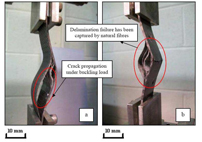
By Dr Hessam Ghasemnejad, School of Aerospace and Aircraft Engineering, Kingston University London, UK