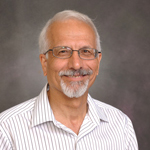
By Ahmad Hemami, McGill University, Montreal, Canada
In the last issue of Windtech International [3] I somehow expressed my worries about whether the future will show an unforeseeable problem with permanent magnet synchronous generators, used in direct drive systems in offshore wind turbines. Now, a different problem, which can be a version of the same type of “unforeseen” problem, has surfaced. I spent a lot of time trying to find out what the problem is, without any success. Digging the internet, I came across a few sites raising the problem(s) with some Siemens-Gamesa turbines, platforms 4.X and 5.X. As Reuters reports, Siemens Gamesa is having “problems affecting up to 15–30% of the more than 132 gigawatts worth of turbines worldwide. Its total wind capacity is equivalent to around 132 nuclear plants.”
However, problems with the above platforms are not necessarily associated with what has happened to the Siemens offshore floating wind turbines, requiring heavy maintenance.
The problem(s) concerned with the floating turbines are associated with five Siemens SWT-6.0-154 direct drive units employed in the very first floating wind farm. According to Siemens-Gamesa brochures, the 4.X and 5.X series are geared turbines and are mainly for onshore wind farms. Furthermore, for the 5.X platform, the prototype was available in 2021, whereas the SWT-6.0-154 model has been in service since 2017. The company has already sold about 300 of its SWT-6.0-154 wind turbines to UK and German projects. Even if all or most of these units are used for offshore wind farms, they are not used with a floating foundation. Also, by October 2023, 2100 units of model 4.X and 800 units of model 5.X have been sold.
From various reports on these 5 turbines in the Hywind floating wind farm, it is obvious that they have been performing very well, at least in the first five years of their service, sometimes probably better than expected. Therefore, whatever could have happened has more likely happened after this period, which points to fatigue in some parts.
From a technological viewpoint it is very important to identify the main issues. If this sort of problem happens to be something similar to the gearbox problem, it is not only Siemens that is involved, and it can be a common problem that other manufacturers can face in due time. In fact, this can be a lesson to learn from. For instance, when major issues cannot be fixed on site and the turbines need to be transported to land for repair, this may become the norm for all future floating wind farms.
What can be understood from the statement of the problem(s) is that
(a) The repair cannot be done onsite.
(b) The turbine must, thus, be towed to land.
(c) It takes four months for the repairs.
It is clear that the problem is not with a small component but with the larger parts, like the blades, the generator, the tower, the foundation, or all of them. Also, extensive repair work is necessary, which requires space and equipment that are not available onsite, or it is more reasonable and economical to bring the turbines to the shore rather than doing the work in the middle of the sea. Moreover, all turbines have the problem(s) and need repair. It must be noted that for certain repair work that is possible for onshore turbines and fixed-base offshore turbines, the motion due to waves may cause the work to be impossible or more difficult for a floating turbine.
What is not clear is whether the estimated four-month period is for repairing all turbines together or one by one. In other words, is the wind farm going to work at a reduced capacity during this period, or does its whole generation come to a halt?
The blades and tower of a floating turbine can be subject to more stress compared to those with fixed base structures. This is due to forces from waves that can shake the whole turbine and create additional motion/acceleration in various parts. The floating turbines in the Hywind wind farm have spar foundations, which may contribute to the severity of wave induced vibrations compared to other floating structures. For spar foundations, modest wave-induced motions at the waterline introduce large translational motions at the nacelle height.
Noting that the blades of SWT-6.0-154 are based on a new design and are 20% lighter, it can be envisaged that a problem with the blades is the most probable, if not the only one. This agrees with the turbine problem addressed in [4] as wrinkles in the rotor blades of the 4.X and 5.X models.
Further Reading
1. Outstanding load factor performance from the world’s first floating wind farm, Modern Power Systems, 16 May 2018: https://www.modernpowersystems.com/features/featureoutstanding-load-factor-performance-from-the-worlds-first-floating-wind-farm-6151857/
2. Equinor marks 5 years of operations at world’s first floating wind farm, 29 Dec. 2022: https://www.equinor.com/news/hywind-5-years-world-first-floating-wind-farm
3. Is Using DFIG in Wind Turbines an Obsolete Technology? Windtech International: https://www.windtech-international.com/windtech-future/is-using-dfig-in-wind-turbines-an-obsolete-technology
4. Wind turbine flaws put Siemens in a headwind, Power Technology: https://www.power-technology.com/features/wind-turbine-flaws-put-siemens-in-a-headwind/?cf-view&cf-closed