- Category: Articles
Everybody Expects It – But Are They Right?
Consolidation within the wind sector has been much discussed over the past 12–18 months due to weakening demand and ongoing price pressure. However, with global demand down and a manufacturing overcapacity already existing, the consolidation of Tier 2/3 wind OEMs into Tier 1 global competitors is not likely unless there are other factors at play. These other factors include leveraging an intellectual property portfolio, gaining strategic access to a market, gaining a manufacturing footprint in an underserved market, or providing some level of vertical integration. In this article, Philip Totaro considers the wind turbine market and OEM outlook for the next 12–18 months, both globally and for different regions of the world.
By Philip Totaro, Principal, IntelStor, USA
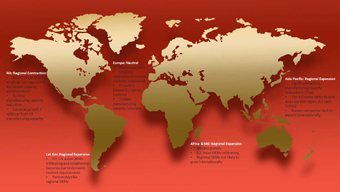
By Philip Totaro, Principal, IntelStor, USA
- Category: Articles
Ultrasonic Wind Sensors Versus Mechanical Anemometers
Making accurate wind measurements in difficult site conditions can be challenging, but the development of the wind energy industry has meant that high quality wind data has become an economic necessity. Multi-million investment decisions are being based on bankable datasets. Over the years mechanical anemometers have become the industry standard for wind speed measurement despite their non-ideal performance in difficult conditions. But with a better understanding of ultrasonic wind sensor functionality, its trade-offs and advantages, perhaps there is now a better way to get these important measurements.
By Nic Wilson and Juha Paldanius, Vaisala, Germany
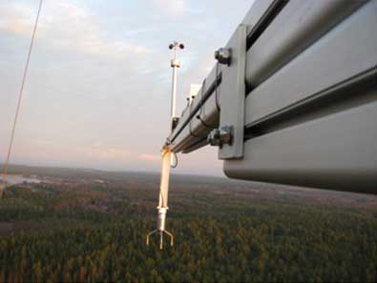
By Nic Wilson and Juha Paldanius, Vaisala, Germany
- Category: Articles
The Maturation of Wind Energy Opposition
An international movement against wind energy is maturing – across the globe today there exist over 1,000 anti-wind groups. The origin of the opposition is, in some instances, fossil fuel and nuclear backed interest groups and, at other times, local community members with genuine concern. Regardless of the source, this burgeoning trend must be dealt with effectively, transparently and compassionately. The alternative: once-trusted company names and brands become vilified, inspiring antagonism and encouraging locals to unify against wind energy projects. This article is the introduction to a series of topical columns which will dig into the causes of anti-wind sentiment and the maturing of opposition against wind energy development, including groups, popular arguments and their proposed countermeasures, as well as an introduction to the spectrum of solutions wind energy professionals can tap to quell what may otherwise become an unmanageable storm of hostility.
By Tiff Thompson, Principal, NIMBY Consulting, USA
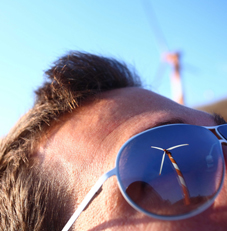
By Tiff Thompson, Principal, NIMBY Consulting, USA
- Category: Articles
Finding the Best Solution for a 5MW Wind Turbine
The power system of the offshore wind turbine is critical to the cost of energy of the installed park. The generator and converter type and configuration are important issues to be addressed during the concept design phase. However, the effects of these choices on the system design and park operation and income are too often overlooked. Annual energy output and system reliability are primary considerations.
By Rain Byars, CEO, Nextwind, Inc., USA
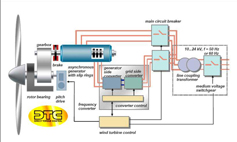
By Rain Byars, CEO, Nextwind, Inc., USA
- Category: Articles
Developing Energy Storage Solutions for the Electric Utility and Transportation Industries
At the most fundamental level, energy storage – like storage in any other supply chain – fulfils a very basic function: it decouples supply from demand. That is, it allows the product to be produced on one schedule and consumed on another. The basic principle that supply and demand should be decoupled governs the design of every major supply chain … except electricity. In this article Steve Hellman, of Eos, talks about the importance of decoupling supply from demand and goes on to explain how Eos’ zinc batteries could help wind and other renewable energy industries with this decoupling.
By Steve Hellman, President, Eos Energy Storage, USA
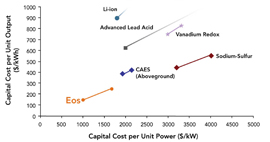
By Steve Hellman, President, Eos Energy Storage, USA
- Category: Articles
Differences in Risk Approach Between Banks and Utilities
The offshore wind farm sector is gaining momentum. New projects with a capacity of 866MW were installed in 2011. However, a uniquely difficult combination of risks has brought about significantly different approaches to project management between banks and utilities. While utilities strive for a high degree of autonomy in terms of structuring the projects, banks call for a direct influence on and total transparency in the project contracts. Understanding these different perspectives will help both sides to cooperate in order to finance the massive pipeline of future projects.
By Simon Matthiessen and Jérôme Guillet, Green Giraffe Energy Bankers
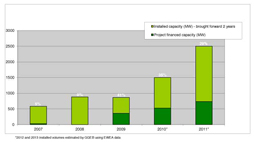
By Simon Matthiessen and Jérôme Guillet, Green Giraffe Energy Bankers
- Category: Articles
First Successful Trial of a Floating Lidar Device in Real Offshore Conditions in the North Sea
A full-size prototype of the floating lidar offshore resource assessment system, known as FLIDAR, has been successfully tested 15 kilometres off the Belgian coast. It was located next to a stationary lidar (WINDCUBEv2 lidar from Leosphere) on a fixed communication mast for the month of October 2011 in order to test survivability and validate the accuracy of the wind speed measurements.
By Bruce Douglas, Sales & Marketing Director, 3E, Belgium
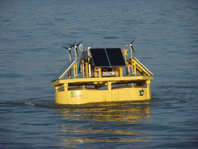
By Bruce Douglas, Sales & Marketing Director, 3E, Belgium
Use of cookies
Windtech International wants to make your visit to our website as pleasant as possible. That is why we place cookies on your computer that remember your preferences. With anonymous information about your site use you also help us to improve the website. Of course we will ask for your permission first. Click Accept to use all functions of the Windtech International website.