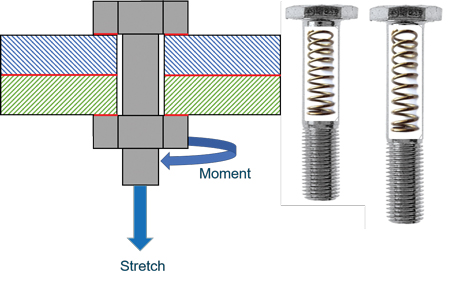
Achieving and maintaining the right tension in bolted joints in wind turbines can help prevent system failures and associated repair costs. One loose bolt in a cluster of several hundred holding a structure together, often interdependently, can cause a domino effect that could, at worst, result in failure of the entire unit. As wind turbines continue to increase in size, the structures need to withstand ever higher centrifugal and bending forces, as well as vibrations – all factors that can affect the integrity of bolted joints. Correct bolt tensioning is, therefore, critical. But, accurate bolt tension is not only difficult to achieve, it can also be difficult to monitor. Danish engineering company R&D has developed an accurate system that uses both mechanical and ultrasonic measurements to determine the desired bolt tension in a way that also saves time. The solution can also digitally track individual bolts throughout their lifetime, ensuring the condition of the bolts is documented.
By Flemming Selmer Nielsen, Senior Specialist Engineer, R&D, Denmark