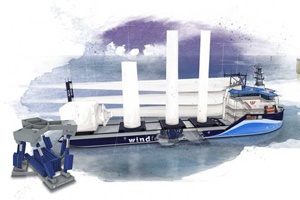
The feeder vessel features a specially designed motion compensation system by Ampelmann. The system uses Ampelmann’s core technology to stabilise the components of the wind turbine generator (WTG) in six degrees of freedom and is designed for safe lifting operations in sea states up to 2.5m significant wave height. The compensator is positioned close to the vessel’s center where it can compensate all vessel motions. The wind turbine components are arranged on the ship with a connect grip- and glide system. Cargo pallets are placed on deck thanks to the quick connect system. Once the feeder vessel is at its destination, the system slides the components into place to connect to the motion compensator. The Ampelmann system then compensates all vessel motions, so the crane operator can lift turbine components in a similar fashion to an onshore lift.