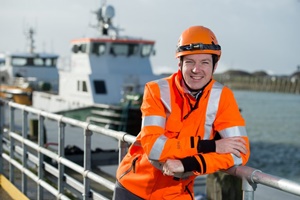
Once fully developed, it will reduce the cost of inspecting and retorquing wind turbine bolts. The project, which is funded by Innovate UK, will develop the existing EchoBolt prototype for deployment and testing at ORE Catapult’s Levenmouth Demonstration Turbine and then on one of GE’s operational wind turbines.
The technology uses ultrasonics to test the tension on the bolts that hold wind turbine structures together. Each turbine has over 1,000 of these critical fasteners, which require regular, manual tests by offshore technicians using heavy-duty hydraulic wrenches. EchoBolt relies on a hand-held ultrasonic inspection device that records sound echoes within bolts, demonstrating exactly when a bolt needs retightening, with the potential to reduce the frequency of bolt maintenance significantly. An additional advantage of the solution is the data it will supply to wind farm operators, allowing them to predict the loss of tension likely on a turbine’s bolts and schedule routine inspections more accurately, reducing unnecessary work days spent offshore. The cost saving for the European wind industry (offshore and onshore) will be an estimated GBP 250 million per year.