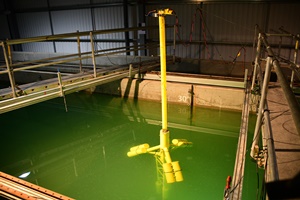
The modelling feeds into work by a consortium to optimise Floating Energy Systems’ (FES) foundation concept. HR Wallingford’s hydraulic specialists have been running tests to allow them to understand the impact of large waves and strong currents on the enormous structures. To run the physical modelling tests, HR Wallingford engineers built a model (1:67 scale) of the Stinger Keel structure. This featured the FES design’s distinctive keel-long for stability in high seas but with a hinged connection so that it fits in the shallower depths of a port from where it can be floated out to its installation site.
Engineers generated a range of wave conditions in HR Wallingford’s Fast Flow Facility to gather data on the model’s behaviour, including examining the strength of the keel’s folding connection. The team also ran tests in the labs for different wind directions and mooring configurations.
The HR Wallingford engineers used data from the physical modelling tests to calibrate and validate two numerical models. These simulations showed the wave pressures exerted on the Stinger Keel foundation structure under a range of conditions.
The team developed two models – a simpler OpenFAST model and an OpenFOAM CFD (Computational Fluid Dynamic) model – to analyse which worked best for which design stage and for extracting information. Initially, the OpenFAST model looks more suitable at early design stages for calculating initial wave and hydrodynamic pressures on the structure. The CFD model is useful in advanced design stages, where more attention to detail is required. The validated CFD model can also be used for future design iterations, without the need for further physical testing. Other consortium partners will use the data gathered from the HR Wallingford tests to perform further structural analysis and refine the design. The consortium’s work, which aims to build confidence in design safety and costs, is due to finish this summer.