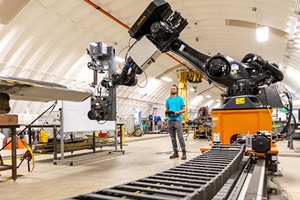
While robots have previously been utilised by the wind energy industry for painting and polishing tasks, automation has not been widely embraced. However, research at the laboratory showcases the capability of robots to undertake trimming, grinding, and sanding of blades. Post-molding operations for wind turbine blade manufacturing typically involve workers perched on scaffolding and clad in protective gear, including respiratory equipment. The introduction of automation, according to the researchers, will enhance employee safety and well-being while aiding manufacturers in retaining skilled labour.
The research was conducted at the Composites Manufacturing Education and Technology (CoMET) facility at NREL’s Flatirons Campus. The robot operated on a 5-meter-long blade segment, although wind turbine blades are significantly longer. Due to their bending and deflection under their own weight, programming a robot to handle larger blade sections would necessitate working on them segment by segment. The researchers employed a series of scans to create a 3D representation of the blade's position, precisely identifying the front and rear sections of the airfoil. Subsequently, the team programmed the robot to execute a sequence of tasks, evaluating its accuracy and speed thereafter. The researchers identified areas for improvement, particularly in grinding, where the robot occasionally removed excessive material in some areas while leaving others insufficiently treated. However, the robot's performance was not compared directly to that of a human undertaking the same functions.
The objective of this research was to develop automation methods suitable for making domestically manufactured blades cost-competitive on a global scale. The finishing process is known for being labour-intensive and often sees a high turnover rate due to the challenging nature of the work. Automating this process could enhance the economic viability of domestic offshore blade manufacturing.
(Photo by Werner Slocum, NREL)