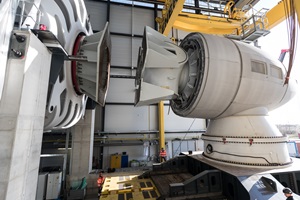
Following on from the test in Bremerhaven, a further test campaign is scheduled to be performed by the project partner RWTH Aachen. It will then be certain to what extent the electrical turbine properties determined in the field test concur with the results from the laboratory test. To date, measurement data from field tests have been used to certify new wind turbine types. As part of the CertBench project, the project partners aim to prove that typical grid faults such as voltage dips and frequency fluctuations can be reproduced just as realistically on a system test bench.
Realistic loads and interactions between the nacelle and rotor will be simulated using real-time models and control algorithms on the test bench for hardware-in-the-loop (HiL) operation. The nacelle is the real hardware on the test bench whilst the rotor is simulated virtually, and the torque is calculated from the flow during testing.
The nacelle from the project partner Enercon has already passed field measurements for its certification. This allows direct comparison of the results determined on the test bench with the available field data. Consequently, validation of the test method becomes possible.