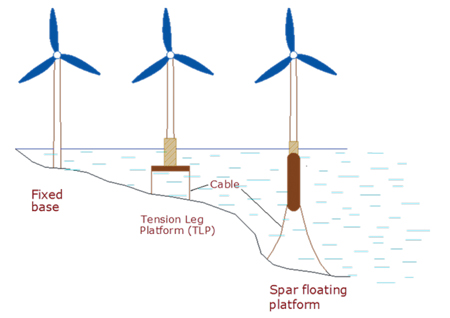
The progress made in the wind energy industry, demonstrated by the design of larger wind turbines to harness more energy from wind, is admirable. All aspects of manufacturing, installation and operation of these giant structures to deliver multimegawatt energy require lots of expertise, ingenuity, determination and hard work. Probably in the beginning no one would have thought of having turbines in the middle of water capturing wind energy, with no complaints about noise, view and other legitimate or illegitimate issues.
By Ahmad Hemami, McGill University, Montreal, Canada
The advancement of technology in this respect has been based on improving and scaling up from smaller turbines. This is an ongoing effort and now we hear about 15MW turbines on the horizon.
Progressing to floating turbines, however, raises the question of whether the floating turbines should mimic those turbines with a fixed foundation.
What is Special About Floating Turbines?
A floating foundation can prove to be less expensive in deeper water. But there is something extra to a floating foundation that we want to discuss here, which future floating turbines can take advantage of.
A floating turbine and its foundation are free to move, although their lateral motions are restricted by cables or chains. What we want to point to is the fact that each turbine is free to rotate about its axis with respect to water. The question is whether we can use this freedom for yawing a turbine, thus eliminating the yaw drive and its associated problems.
The main problem in yaw systems stems from the fact that the yaw ring motion requires a precise contribution from each participating motor in a very synchronised manner. Otherwise, the drive and the driven meshing teeth can stay under unnecessary stress, sometimes working against each other. Such a situation can continue for the periods between two yaw operations, although during this time the yaw brakes are applied. If the whole turbine is yawed, this problem is removed.
An Alternative Yaw Motion for Floating Turbines
The alternative option available only to floating offshore turbines is to yaw the whole turbine (including the tower and the foundation) with a set of thrusters that are attached to the foundation below the water surface. The advantage is that the operation of these actuators, although simultaneous, is independent of each other. They are not going to work against each other or cause overstress. The trade-off is a higher torque demand for the manoeuvre since a higher mass needs to be moved. On the other hand, the friction forces in the yaw system disappear. Also, the weight of the whole yaw system is removed from the tower top.
As for comparison and estimating the order of magnitude of the essential torque if this strategy is used, some calculations are carried out for a 6MW turbine. The corresponding data for mass and other parameters/dimensions are taken from the literature when available, otherwise estimates are made for them based on analogy. The following data are used for this purpose:
- Blades: 3 × 25 tonnes, 75 metres
- Tower: 670 tonnes
- Foundation: substructure: steel (14.5-metre diameter, 91 metres long), 2,300 tonnes; when ballasted 10,000 tonnes, 78 metres below sea level
- Rotor diameter: 154 metres, 300 tonnes (estimated)
- Nacelle: 300 tonnes (estimated).
A yaw speed of 0.25°/s (15°/min) to be reached in 5 seconds is considered. For this rotational speed, a complete revolution takes 24 minutes.
A spar foundation is the best from the viewpoint of the manoeuvring effort. Also, the effect of the water viscosity is minimum for a single unit cylinder. For our example, although the contact surface with water is a cylindrical body with a height of 78 metres and diameter of 14.5 metres, because of the low rotational speed, the resistance of water to motion is very small and negligible. The essential inertial torque for moving the 11,800 tonne foundation and tower makes the principal element for selection of the underwater thrusters.
For this example the required torque, based on the inertia only, is 6.4 times that of the torque for overcoming the inertia of the rotor and nacelle. This number, nevertheless, is very crude and does not include the friction forces in the current yaw system, which cannot be ignored. Consequently, in a real scenario the ratio of the required torque based on the new idea to the torque in the present system might be quite smaller.
If eight thrusters at a radius of 8 metres from the spar centre line are employed, the thrust required to provide the torque for yawing the entire turbine in the example is 4,748N each.
The numbers given here exemplify the net torque and force (thrust) values without considering the efficiency of the involved machinery.
Summary
Offshore floating foundations have the extra advantage that they allow omission of the yaw system from wind turbines. As well as eliminating the problems with the yaw system, there is a reduction in the tower top weight of the yaw ring, motors and braking equipment. This advantage may prove to be worth the effort for future deep-sea offshore turbines.