- Category: Articles
How to Build Tomorrow's 12MW Turbine with Components Available Today
The 5 to 7MW range turbine is the upper end of what you can achieve by enlarging megawatt-scale architecture, but it is an awkward size range. The weights are high, the installation equipment is not commonly available and the cost of energy is not on a par with 1 to 3MW onshore installations. The question is how can we upscale beyond this awkward limit, and bring costs back down? The Nextwind Gaia architecture overcomes the barriers to upsizing existing wind turbine technologies, and aims to make possible large-scale offshore wind plants which will beat the initial cost, and cost of energy, of land-based wind farms.
By Rain Byars and William Miller, Nextwind, USA
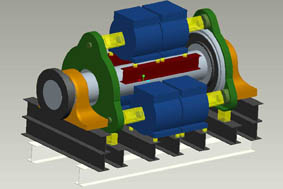
By Rain Byars and William Miller, Nextwind, USA
- Category: Articles
Reducing the Cost of Energy by Reducing Overall Cost of the System
Researchers at Cleveland State University (CSU), an urban school in Cleveland, Ohio, have designed a wind tower system that is aligned with the small distributed wind energy systems initiative of Energy Efficiency and Renewable Energy of the US Department of Energy. The patented system is designed to facilitate the conversion of wind energy into useable electricity at locations where the wind speed is relatively low, and where conventional wind turbines do not yield significant amounts of electrical power. One of the goals of this research project at CSU is to reduce the cost for generating electricity via reducing the overall cost of the system. As a result of the unique modular attributes of the design the system can be scaled up along its vertical axis, while at the same time keeping its footprint and the size of its individual turbines unchanged for different targeted power ratings.
By Dr Majid Rashidi, Cleveland State University (CSU), USA
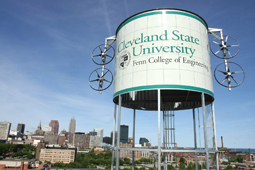
By Dr Majid Rashidi, Cleveland State University (CSU), USA
- Category: Articles
Direct Detection Lidar for Wind Measurement
Wind-sensing lidars are considered a promising technology for the high quality wind measurements required for different applications such as hub height wind resource assessment, power curve measurements and advanced, real-time, forward-looking turbine control. Until recently, the only available lidar technology was based on coherent Doppler shift detection, whose market acceptance has been slow primarily due to its high price. Direct detection lidar technology provides an alternative to remote sensing of wind by incorporating high precision measurement, a robust design and an affordable price tag.
By Nathan Sela PhD, co-founder and VP of R&D, Pentalum Technologies, Israel
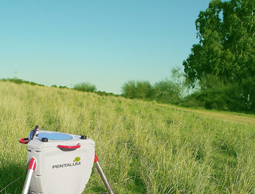
By Nathan Sela PhD, co-founder and VP of R&D, Pentalum Technologies, Israel
- Category: Articles
High-Resolution Meteorological Data to Plan the Placement of an Offshore Wind Grid
Using a sophisticated weather model, environmental engineers at Stanford University (USA) have defined the optimal placement of a grid of four wind farms off the US East Coast. The model successfully balances production at times of peak demand and significantly reduces costly spikes and zero-power events.
By Andrew Myers, Associate Director of Communications, Stanford University School of Engineering, USA
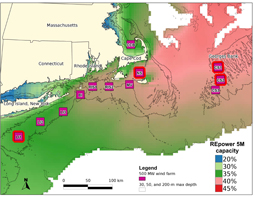
By Andrew Myers, Associate Director of Communications, Stanford University School of Engineering, USA
- Category: Articles
How Ice Accretion Affects Wind Turbines
For the wind energy industry a 'cold climate' site refers to a location that might experience significant periods of time or frequency of icing events or low temperatures outside the operational limits of standard wind turbines. In recent years many countries in Europe, Asia and North America have had to develop wind farms in cold climate regions. The main reasons for this choice are good wind energy resources in high altitudes (e.g. Switzerland with sites at 800 metres above sea level), and the higher installation and O&M costs for offshore when compared with land-based wind farms. This new development has brought some new challenges for designers, manufacturers and operators. One of these challenges is icing of the wind turbine blades and its effects on the aerodynamics and responses of the wind turbine. This article addresses ice accretion on the blade and its effects on the aerodynamic properties of the rotor.
By Mahmoud Etemaddar, PhD candidate, Institute of Marine Technology, NTNU, Norway
For the wind energy industry a 'cold climate' site refers to a location that might experience significant periods of time or frequency of icing events or low temperatures outside the operational limits of standard wind turbines. In recent years many countries in Europe, Asia and North America have had to develop wind farms in cold climate regions. The main reasons for this choice are good wind energy resources in high altitudes (e.g. Switzerland with sites at 800 metres above sea level), and the higher installation and O&M costs for offshore when compared with land-based wind farms. This new development has brought some new challenges for designers, manufacturers and operators. One of these challenges is icing of the wind turbine blades and its effects on the aerodynamics and responses of the wind turbine. This article addresses ice accretion on the blade and its effects on the aerodynamic properties of the rotor.
By Mahmoud Etemaddar, PhD candidate, Institute of Marine Technology, NTNU, Norway
- Category: Articles
High-Resolution Digital Photography for Offshore Aerial Bird Surveys
As a result of the rapid growth in the offshore wind sector, the demand for spatial environmental data is constantly increasing. Traditional visual aerial survey methods suffer from reliability, safety and data quality drawbacks. These can be overcome by new digital methods, and in this article we discuss the application of these new technologies to offshore aerial bird and mammal surveys.
By Stuart C. Clough, Director of Remote Sensing, APEM, UK
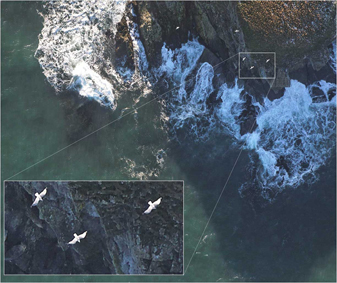
By Stuart C. Clough, Director of Remote Sensing, APEM, UK
- Category: Articles
Techniques for Addressing Larger Wind Farms
Layout tools attempt to identify the best layout of wind turbines on a land or offshore area according to energy capture. They model free stream wind flowing through an area with sited turbines and calculate the energy output of successive turbines while taking wake effects and turbulence intensities into account. A key component of such tools is the ‘optimiser’ algorithm used to efficiently search through a modest proportion of candidate layouts to identify the best one. This article discusses earlier bio-inspired algorithms, and then the CMA-ES algorithm, an evolutionary algorithm that performs stochastic sampling optimisation by mimicking fundamental aspects of the neo-Darwinian evolutionary process.
By Kalyan Veeramachaneni and Una-May O’Reilly, Evolutionary Design and Optimization Group, CSAIL, MIT, USA
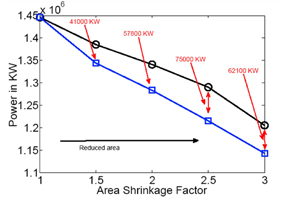
By Kalyan Veeramachaneni and Una-May O’Reilly, Evolutionary Design and Optimization Group, CSAIL, MIT, USA
Use of cookies
Windtech International wants to make your visit to our website as pleasant as possible. That is why we place cookies on your computer that remember your preferences. With anonymous information about your site use you also help us to improve the website. Of course we will ask for your permission first. Click Accept to use all functions of the Windtech International website.