The RIWEA Project
In order to keep a wind power plant in operation reliably, regular maintenance work is essential. The rotors, in particular, bear enormous mechanical stress and therefore require regular periodic checking for failures. Currently, this work is done manually by technicians rappelling from the top of the wind turbine, or by using a crane from the ground, or from a manually operated working platform. The inspection of the blade surface is done visually and with simple tapping tests. If a surface area looks conspicuous, it is examined afterwards by ‘coin tapping’. If blade damage is identified, high costs may quickly arise due to extensive repair work and long downtime. This article presents the development of a special self-propelled robot, which enables inspections on the surface of a wind turbine’s rotor blades to be carried out mechanically.
By Tilo Förster, Torsten Felsch and Norbert Elkmann, Fraunhofer IFF, Germany .
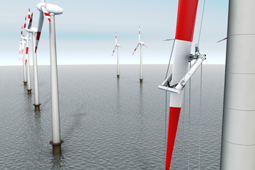
By Tilo Förster, Torsten Felsch and Norbert Elkmann, Fraunhofer IFF, Germany .