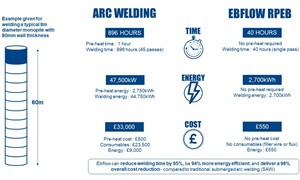
It will be the first time RPEB has been used on a large-scale offshore infrastructure project and has come about as part of a collaborative partnership named RapidWeld. Ebflow RPEB uses heat generated by a beam of high-energy electrons to make a high strength and durable welded steel join. The RapidWeld project team comprises of: SSE Renewables; Aquasium Technologies (trading as Cambridge Vacuum Engineering), the SME designer and manufacturer of the RPEB equipment; Sif, a manufacturer of offshore foundations; and, TWI, a UK welding research establishment. Sif will be responsible for the fabrication and supply of 190 monopiles and primary steel for the transition pieces, as well as for the marshalling of all foundation components for the first two phases of Dogger Bank Wind Farm.