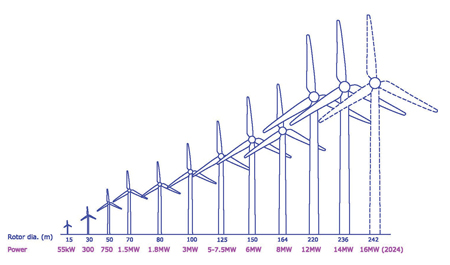
By Ahmad Hemami, McGill University, Montreal, Canada
All the technological advancements during the last 40+ years undoubtedly demonstrate the results of good efforts. This progress is represented in the increased turbine size and energy capture. Figure 1 shows this growth for typical turbines. Compared with a coal-fired power plant, a 5MW turbine, for instance, reduces carbon dioxide emission to the atmosphere by 28 tons per day (about 17 tons for natural gas). That is what we need; that is the good.
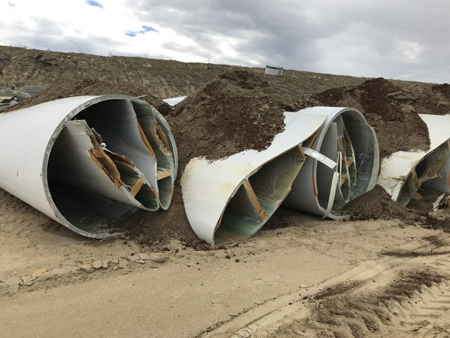
The ugly is well represented by the landfill in Figure 2. The best thing that the wind turbine manufacturers can do, and that is a real advancement, is to find solutions to this problem. I was so delighted to find out that at least three of the large manufacturers are working in this direction. Recycling is the solution. In the past, recycling was rarely considered. Everything was put into the rubbish/waste, and unfortunately there are places where this still happens. Eventually, we realised that we cannot selfishly pile up our waste on land and in the sea forever. This applies to many man-made products, including wind turbines. We cannot just continue to build more and more of something and then throw it away afterwards.
Recycling can be (initially) costly but it is the best way (if not the only way) to tackle this man-made problem. The hidden cost added to a product to take care of the rubbish and pollution should not be ignored. Only responsible companies/governments/people pay attention to it. Ignoring cleaning up is an irresponsible action.
Manufacturing without considering recycling is the same as what happens in mining when ignoring (leaving behind) plenty of an orebody because it is of a lower grade and its removal involves a more costly process. This maximises the profit but ignores the long-term effects. This is shown in Figure 3. All the ore with a grade below 0.15%, for example, can be left in the abandoned mine, although there is still plenty of the mineral in the deposit.
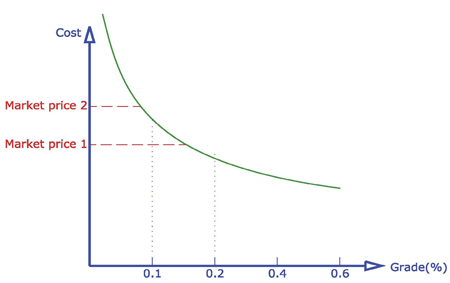
For wind turbine recycling, Vestas and Siemens Gamesa have found ways to separate the resin from the other components to make it possible to reclaim the glass, carbon fibre, wood, etc. GE, on the other hand, considers the alternative application of using crushed turbine blades for mixing with asphalt or other construction materials.
Further Reading
- Barsoe, T. 17 May 2021. End of wind power waste? Vestas unveils blade recycling technology. (https://www.reuters.com/business/sustainable-business/end-wind-power-waste-vestas-unveils-blade-recycling-technology-2021-05-17/)
- Siemens Gamesa Renewable Energy. 2021. Recyclable blade. Taking responsibility. Blade by blade. (https://www.siemensgamesa.com/en-int/-/media/siemensgamesa/downloads/en/sustainability/environment/siemens-gamesa-20210901-recycableblade-infographic-finalen.pdf)
Yang, Y. et al. 2012. Recycling of composite materials. Chemical Engineering and Processing 51, 53–68.