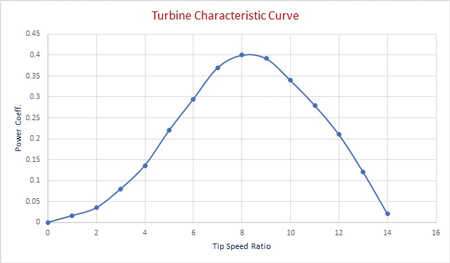
By Ahmad Hemami, McGill University, Montreal, Canada
Noting the reliability problem with power converters, especially when handling larger powers, the question can be asked whether having back-to-back converters to switch from rectifier to inverter is really worth it, or can it make them more susceptible to early failure? According to personal conversations with the managing director of a company in the wind turbine maintenance business, 60% of the company’s repairs are on power converters. In a previous article (Windtech International, Vol 17, No. 4) I pointed to the fact that, as studies show, power converters have some reliability issues. In such case, it is more advisable to minimise the possible sources of stress on these components.
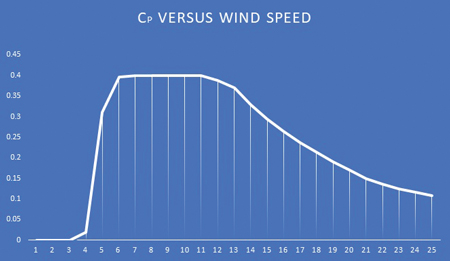
In this study, it is shown that the additional power production in the range of wind speeds between 3 and 5m/s in a turbine equipped with a DFIG and operating at variable speed is less than 1% of the production of the turbine. For this study, a 3MW turbine is considered to work in two typical onshore wind regimes, with 7 and 8m/s average wind speeds. Since no actual data for the turbine performance curve is available from the manufacturer, reasonable simulated data is used, which confidently represents a typical turbine. Also, for the wind regime, Weibull model data is employed, which is widely acceptable.
Figure 1 shows the performance curve of the turbine. The turbine rotor has a diameter of 100 metres and the cut-in and cut-out speeds are 3 and 24m/s, respectively. For wind speeds smaller than 5m/s the turbine rotates at 8rpm (tip speed = 41.9m/s) and for wind speeds larger than 11m/s it rotates at 16rpm (tip speed = 83.8m/s). For 5 < v < 11m/s the rotation speed is optimised accordingly for the best tip speed ratio (l = 8). Figure 2 shows the power coefficient versus wind speed for a turbine operating at variable speed.
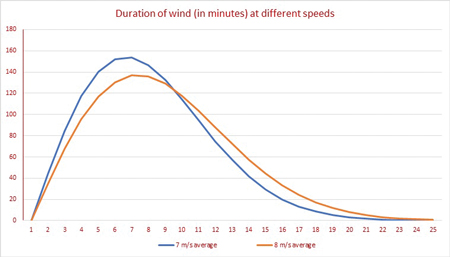
The last column in the table is the equivalent number of days for the yearly production for this portion of wind speeds (3–5m/s) based on 300 days, assuming 60 no-wind days and 5 maintenance and forced outage days.
We observe that in a turbine with a DFIG, one mode of operation counts for less than 1% of production. Also, from a control perspective, additional hardware may be associated with the switching capability. If this switching between sub-synchronous and super-synchronous operation puts extra stress on these components and makes them more vulnerable to failure, a possibly overlooked question arises. Is it worthwhile to work in two modes or is it better for the converters to always work in one mode?
Wind (average, m/s) | Daily energy (MWh) | 3–5m/s portion (kWh) | % ratio | Equivalent number of days per year |
7 | 23.55 | 228 | 0.97 | 2.90 |
8 | 28.97 | 190 | 0.66 |
1.97
|
Table 1. Summary of energy calculation