- Category: Articles
How Collection System Cabling Impacts the Finances of a Project

By Lucas Cook, NEI Electric Power Engineering, USA
- Category: Articles
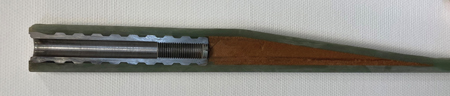
For wind turbine blades, generally two main root connection types exist to connect the rotor blade to the hub of the turbine: the T-bolt connection or bushing technology. Where for small size rotor blades both connection types are frequently used, for the large multi-megawatt turbines the bushing connection technology is becoming very interesting because of the potential to have longer blades with smaller roots.
By Edo Kuipers, We4Ce, the Netherlands
- Category: Articles
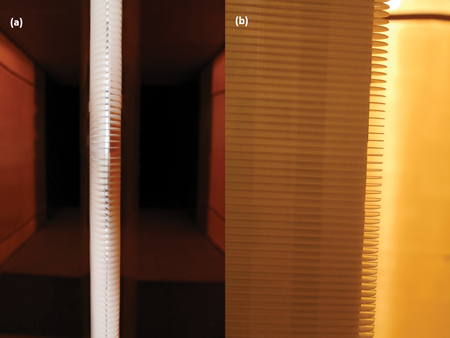
Some species of owls have long been investigated for their ability to fly silently. This led to the discovery of several wing attributes that differ from other birds of prey. Trailing edge serrations, a now common wind turbine noise reduction technology, are derived from one of these features – the fringe along the downstream edge of the owl’s wing. A group of researchers from Virginia Tech, Lehigh University, Florida Atlantic University and the University of Cambridge have developed a novel noise reduction technology for airfoils based on another feature – the soft downy coating on the bird’s feathers. Results indicate that this new technology can reduce airfoil noise by up to 10 decibels. Additionally, this concept can be deployed in combination with serrations to further reduce the noise produced by wind turbines.
By W. Nathan Alexander, Assistant Professor, Virginia Tech, USA
- Category: Articles
Pitch Health Indicator for Static Pitch Misalignment of Rotor Blades
Rotor blades pitch above nominal wind speed to limit the loads on the turbine. Below nominal power, there is no pitch control. As much as possible power is extracted from wind by optimising rotor speed. However, a design angle of attack must be respected, supposing a correct reference pitch angle. Misalignment can result in aerodynamic imbalance with increased fatigue loading and potential reduced performance.
Pitch misalignment can be absolute (blade vs design position) or relative (blade vs another blade). The GL 2010 Guideline provides acceptable values for absolute and relative (0.6°) misalignment. Around 25% of turbines suffer from misalignment above 0.6°. Field campaigns can be time-consuming and the risk of targeting healthy blades is significant. Therefore, a Pitch Health Indicator (PHI) has been developed by scrutinising SCADA data. The PHI helps to prioritise the turbines to be investigated/corrected in a cost-efficient way in the field.
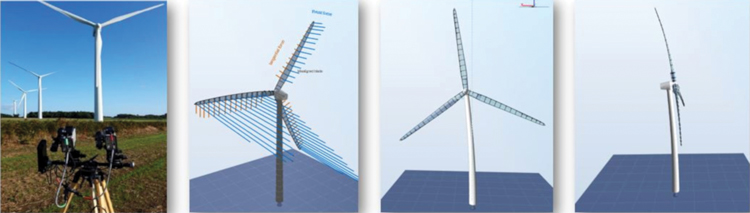
By Nicolas Quiévy, Julien Masson, Fiona Buckley, Olivier Van Oost, Stephane Bronckers, Belgium
- Category: Articles
Aiming Towards Environmental and Economic Improvements Through Chemical Recycling
Wind turbine blade waste is becoming an increasing problem as the first generation of turbines is now being decommissioned and the blades are ending up mainly in landfill, incineration and the cement industry. The annual volume of this waste in Europe alone is expected to increase from 40,000 tons to 120,000 tons in the next 10 years.
The wind, composite and chemical industries consider it important to improve the circularity of blades, and new innovations in chemical recycling could play a part in that. The goal of Interreg North Sea Region funded project, DecomTools, is to decrease the costs and environmental impact of the decommissioning of offshore wind farms. The chemical recycling of blades is expected to play an important role in meeting those goals. Therefore, Dutch recycling company Virol will be testing it at a pilot scale as part of the project.
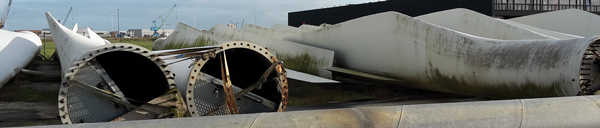
By Nina Vielen-Kallio, New Business Manager, Virol, the Netherlands
- Category: Articles
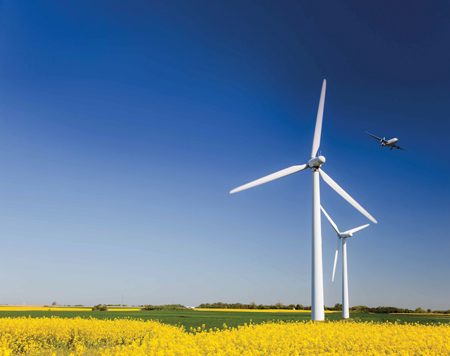
While the need for renewable energy grows ever stronger and the energy market exploits wind power, the locations available for building wind farms without impacting airports and military bases due to radar interference are rapidly dwindling. Wind turbines can appear as clutter on radar screens, obscuring incoming aircraft, spawning false plots and even interfering with storm and precipitation predictions, making for unsafe landing conditions.
By Adam Nevin, Innovation Lead, Trelleborg Applied Technologies, UK
- Category: Articles
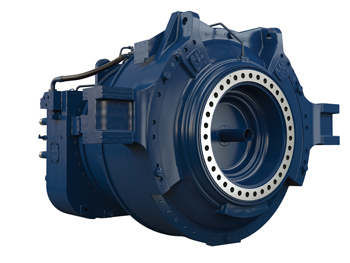
Sensing360 recently released ‘the smart photonic sleeve’ to monitor the load applied on rotating equipment, like bearings and gears. Besides the standardised smart sleeve that serves a broad range of load sensing applications, the company’s fibre-optic sensing technology can also be used for customer specific solutions. Here we show a customer case where Sensing360 has provided a solution to monitor and verify strain levels in the stationary outer ring of a multimegawatt planetary gearbox. Algorithms have been developed that translate these strain signals into crucial engineering and operating parameters such as planet load sharing and torque.
By Georgo Angelis, Sensing360 and Unai Gutierrez Santiago, Siemens Gamesa
Use of cookies
Windtech International wants to make your visit to our website as pleasant as possible. That is why we place cookies on your computer that remember your preferences. With anonymous information about your site use you also help us to improve the website. Of course we will ask for your permission first. Click Accept to use all functions of the Windtech International website.