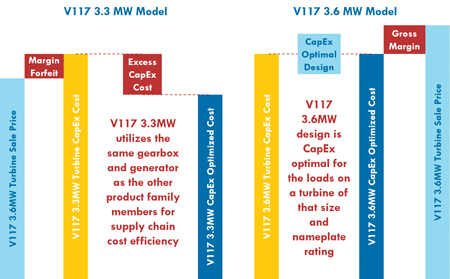
The era of auctions and tenders is well and truly upon the wind energy industry, and the supply chain is already starting to feel the pinch. Some companies have reported tighter and in some cases negative margins in their Q3 and Q4 quarterly financial disclosures as they reconcile their business with a largely subsidy-free era.
By Philip Totaro, Founder and CEO, IntelStor
Some of these companies have taken steps to gain more cost efficiency from scaling their subcomponent orders by changing the way their product portfolios are designed. As we examine a company such as Vestas, for example, we find that there are some distinct benefits to supply chain cost optimisation resulting from this shift in product design that are not obvious at first glance.
This new modular turbine design philosophy implies that if you have a set of wind turbines with different rotor sizes for distinct wind classes which can be rated at 3.3, 3.45 or 3.6MW in nameplate capacity, and all models are utilising the same or very similar subcomponents, then not all of the turbines in that product family have necessarily been designed for an optimal capex cost or levelised cost of energy (LCOE) on an individual turbine basis.
The reason for this suboptimal cost profile for some models is that since all subcomponents in this 3.3–3.6MW product family must be designed to accommodate this range of nameplate capacities, the turbines must be designed for the worst-case loads in mind. The worst-case loads for this particular product family are at the highest nameplate power rating of 3.6MW.
The implication is that the turbines which share a number of the same subcomponents, like generators or gearboxes, have those components overdesigned for the smaller nameplate power ratings. This overdesign comes in the form of extra material usage (and thus extra capex) for the worst-case physical loads that a 3.3MW turbine would experience in a normal operational environment.
As a result, profit margins are sacrificed on projects where turbines are at 3.3 or 3.45MW power ratings due to this excess material in the drive-train and tower due to the design for 3.6MW series loads. So why would OEMs make this sacrifice to optimise a turbine for capex cost on the smaller turbines in the product family? Because the money is made back on supply chain contracts due to this commonality of components across the 3.3–3.6MW product family.
In this case, Vestas has a series of at least 15 different products ranging from the V105-3.3 to the V136-3.6 which all share a common pool of subcomponents. This lowers the supply chain costs due to increased order volumes for subcomponents across a pool of products more widely sold around the world versus the need to have manufacturing tooling for multiple individually optimised turbines which have no component reuse.
This approach also simplifies and reduces O&M costs thanks to reuse of components, which necessitates less stockpiling. There is a similar implication for their 3.8, 4.0 and 4.2MW product portfolio as well, which also shares subcomponents using the same philosophy as the 3.XMW.
But there is another unseen benefit to the smaller turbines in a product family as a result of this ‘overdesign’. Despite suboptimal capex/LCOE on some turbine models in a product family, the product models which have a smaller nameplate power rating also have an extra loads envelope due to this component overdesign for loads. As a result, these turbines can be:
- run ‘harder’ during the normal turbine lifetime, and/or
- accommodate a wider array of project sites with increased turbulence intensity (i.e. also a potentially higher fatigue loads capacity over the lifetime of the turbine), and/or
- they can delay the need for life extension technologies or repowering due to an extra built-in component reliability due to the extra loads margin.
Because more project developers are seeking turbines at the higher power ratings to optimise investment returns on projects, the commercial impact on Vestas is relatively minimal because more turbines are being sold in ‘power optimised mode’ at 3.6MW versus 3.3 or 3.45MW.
The end result is a product portfolio which is capable of being sold in all countries and in all wind regimes with fewer specialised components for each turbine make or model. The modular architecture and reuse of components means that the Vestas product portfolio is now capable of being manufactured and sold globally in a cost-effective manner.
With a shift towards auctions/tenders globally, the supply chain will need to employ clever strategies such as this to continue to maintain profitability. Those companies who do not understand the implications of this design philosophy, or choose not to replicate it, will potentially find themselves consolidated out of an increasingly competitive and global market.