- Category: Articles
![]() |
![]() |
Because wind turbines operate in the natural atmosphere, high-resolution weather modelling is a powerful tool to help wind energy projects succeed throughout the project life cycle. When properly applied, such modelling helps to optimise wind farms by reducing the uncertainty associated with the spatial variability of wind flow across the site. Studies have shown that the uncertainty of mesoscale modelling for wind energy, when run at microscales, is lower than that of other modelling techniques such as linear flow models and computational fluid dynamics. Key features in the underlying physics and application technique of mesoscale models compared with the other modelling methods result in higher accuracy for wind energy assessment. Those differences are described herein. Additionally, we present validation statistics for a large dataset of wind projects to explore relationships between model error and other model and site parameters.
By Gregory S. Poulos and Mark Stoelinga, ArcVera Renewables, USA
- Category: Articles
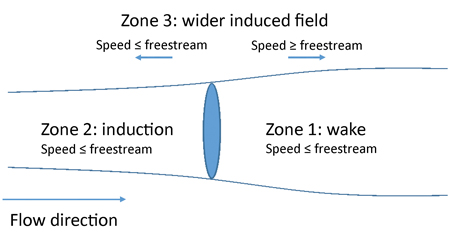
The notion of wind farm blockage has recently created significant debate and raised many unanswered questions within the wind industry. Does blockage actually exist? Could it explain historical differences between pre-construction and operational yield assessments? What should we do about it? Here Frazer-Nash provides some of the latest thinking about understanding and predicting blockage.
By Graham Hawkes, Engineering Manager, Frazer-Nash Consultancy, UK
- Category: Articles
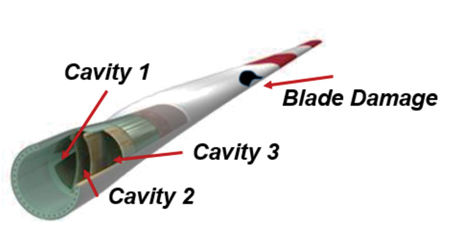
It has recently been shown by the team at the University of Massachusetts Lowell that the acoustic signature generated by a turbine itself can be used to detect blade damage. This acoustics-based blade structural health monitoring approach will help minimise blade failures and lower the levelised cost of energy through a reduction in O&M costs. The proposed solution consists of low-cost, easy-to-implement acoustic sensors and a central data processing and wireless data transmission unit. The monitoring solution can be installed on both new and existing wind turbines.
By Murat Inalpolat, University of Massachusetts Lowell, USA
- Category: Articles
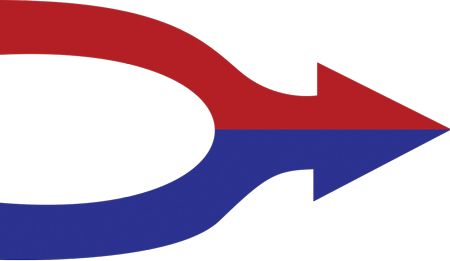
ENTR is an industry alliance set up to promote open-source standards within the wind sector. Among its participants are leading owner-operators, software vendors, a trade association, and a governmental organisation.
By Charles Henderson, CEO, Stacker Group, USA
- Category: Articles
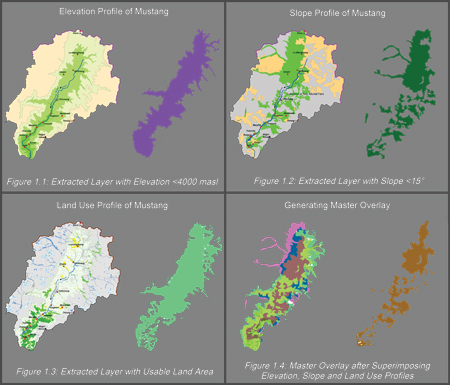
A high cost of licensed micro-siting software, a lack of reliable ground-based wind resource data and difficulty assessing geographically morphed areas of the country make it challenging for project developers in Nepal to perform preliminary siting and tangible evaluations of large-scale wind projects. Furthermore, areas with the most promising wind resource profiles in Nepal are usually located in rural and remote regions with poor accessibility and limited aggregated geographical data, and they are often isolated from electrical grid infrastructures. As such, identification of suitable locations for developing wind projects requires complex multi-criterion analysis, which in turn requires upfront investment. This article elaborates on a necessity-driven framework for wind farm siting and sizing that can process freely available project-specific parameters, geospatial data and factual information to identify project locations and produce quantitative figures for electricity generation.
By Ayush Acharya, WindPower Nepal, Nepal
- Category: Articles
Reducing the Maintenance Cost of Electrical Parts and Controls
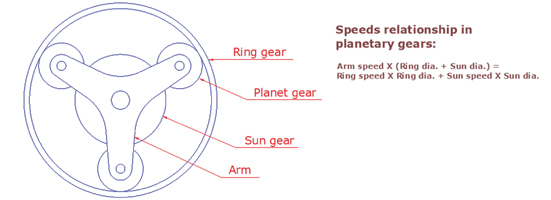
By Ahmad Hemami, McGill University, Canada
- Category: Articles
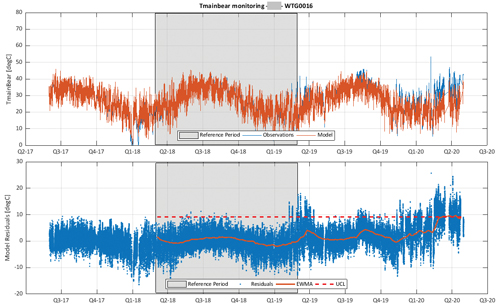
In the quest to further reduce the levelised cost of energy, condition monitoring (CM) and advanced analytics (AA) approaches play predominant roles. Differing in their requirements, costs and scope they are typically considered separately and not in combination. In best-case scenarios, analysts in each field work in silos rather than in collaboration. However, asset owners and operators have always been pushing towards a unified and integrated source of data to inform their O&M operations. Given the ever-decreasing cost of cloud-based storage and processing one could imagine that they may be getting closer to this. In the meantime, there are a few simple ideas worth exploring to get CM and AA analysts closer to achieving that goal.
By Dariush Faghani, Senior Engineer, Power Factors, USA
Use of cookies
Windtech International wants to make your visit to our website as pleasant as possible. That is why we place cookies on your computer that remember your preferences. With anonymous information about your site use you also help us to improve the website. Of course we will ask for your permission first. Click Accept to use all functions of the Windtech International website.