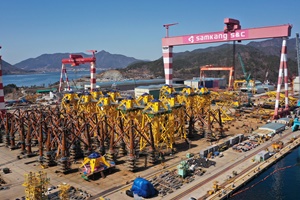
For this offshore wind farm, 21 jackets of 60 m high, weighing more than 1,100 tonnes each and comprising all together more than 23,000 tonnes of steel are being manufactured at the South Korean Shipyard Company Samkang. Construction started in the summer of 2019 and the first jacket will be completed by the second half of April. The jackets include the Transition Piece (TP) for the installation of the 5.2MW turbines. The TPs have a maximum diameter of 5.40 m and a maximum height of 7 m.
Each jacket will be attached to the seabed by means of 4 pin piles. The pin piles with a diameter of 3 m, a maximum length of 82 m and maximum weight of 310 tonnes, are manufactured at a South Korean fabrication yard managed by the Scottish company Edgen Murray. First load-out is planned in mid-April. A number of pin piles have been manufactured in Taiwan by the steel fabricator Ming Rong Yuan Business.
The 21 jackets will be transported in five batches from South Korea to Taiwan. A first batch of four jackets will depart to Taiwan in the first half of May. A 1,500 tonnes crane vessel will lift them onto a heavy transport vessel which will sail to Taichung Port. From there, the jackets will travel to their final destination off the coast of Fangyuan.
Jan De Nul Group is responsible for the design, fabrication and installation of the foundations, the installation of the wind turbines, the supply and installation of the cables off- and onshore as well as for the upgrading of the electrical substation. Hitachi is in charge of manufacturing, assembly and other works related to the offshore wind turbines which will have a downwind rotor. The consortium, consisting of Jan de Nul and Hitachi is responsible over five years for the operation and maintenance (O&M) of the offshore wind farm.